GREEN BAY, WI
FedEx Freight Facility

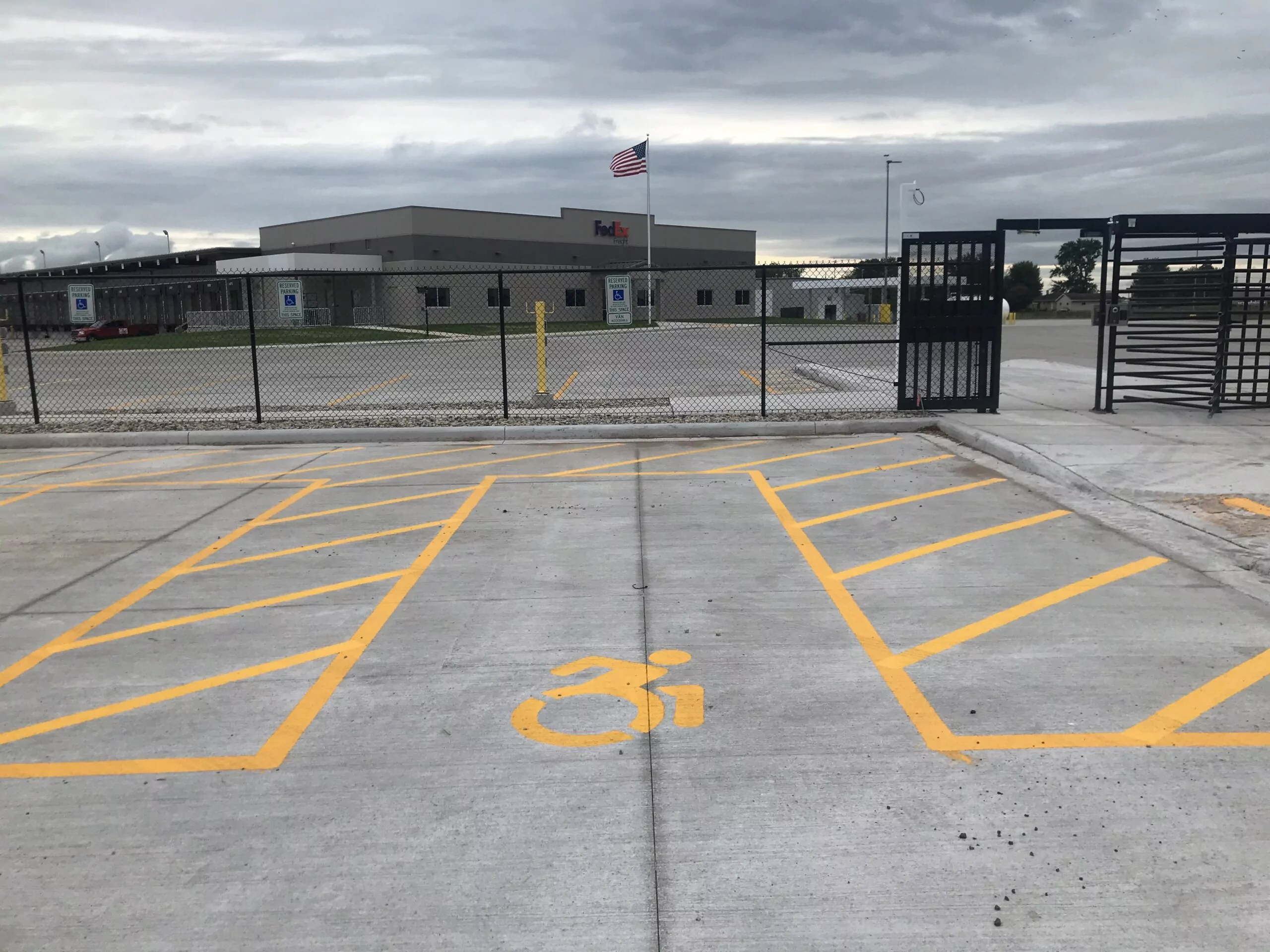
THE PROJECT
A 31-acre farm field is the site for FedEx Freight’s LEED-certified (WDC v4), 72,444-gross-square-foot distribution center with cross-deck bays and office areas. Paladin provided LEED administration and whole building commissioning for the project.
The decision to proceed with LEED was reached later in the project. The team engaged the LEED process aggressively to meet required deliverable timelines and LEED milestones while satisfying FedEx Freight’s design standards. To achieve maximum sustainability with minimal cost or schedule impacts, Paladin focused on system performance, materials, and occupants.
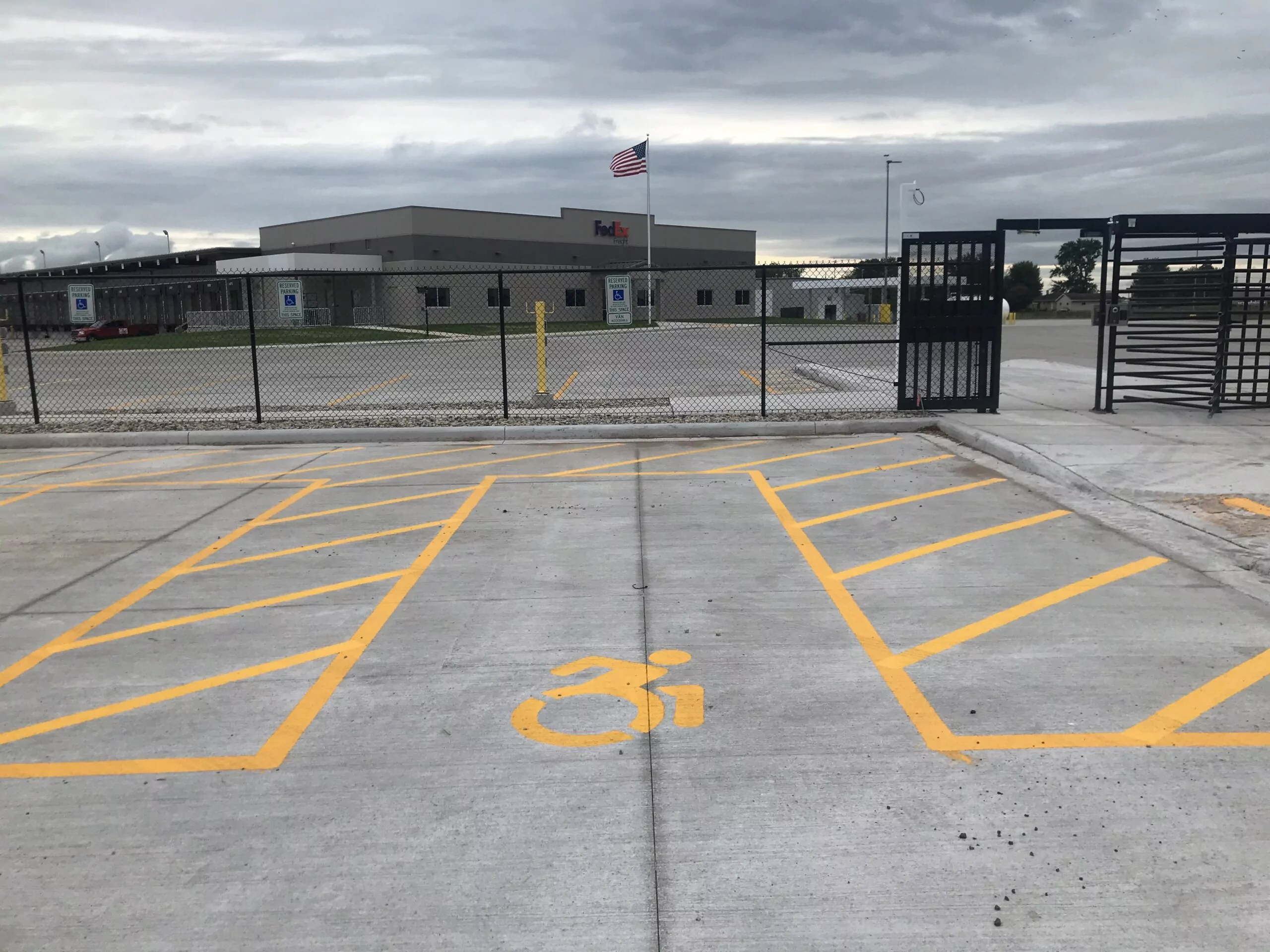
THE WORK
EMISSIONS REDUCTIONS
While still providing occupant comfort throughout the office and dock areas, the prevalent usage of LED interior and exterior lighting as well as efficient electric HVAC systems allowed for a 45.6% energy cost reduction over baseline (2,090,959 kBTU/year).
The inclusion of WaterSense plumbing fixtures reduced potable water consumption by 30%, while reliance on native plantings allowed the project to remove planned irrigation systems. The changes accounted for a savings of 478,659 gallons of water annually.
The project emphasized the embodied carbon of products selected, optimizing the foundations and building assemblies to reduce CO2.
INDOOR ENVIRONMENTAL QUALITY
Considering the health and well-being of those working in the facility was of great importance to the FedEx Freight team. Strategies to improve air circulation in the dock areas coupled with HVAC zoning in the offices allow for greater thermal comfort. Enhanced interior lighting improves the ability of personnel to perform tasks effectively while enhancing safety. To protect personnel from fumes and contaminants, the project used a series of strategies from “no truck idling” to electric forklifts to source separation of exhaust streams to low-emitting materials. These investments will have a daily impact on the lives of the team members serving FedEx Freight’s customer base.
COMMISSIONING
The project included building commissioning to ensure that energy-consuming and building enclosure systems perform to project requirements. Maintainable and operational design reviews, equipment reviews, and performance testing preceded training and legacy documentation delivery.
MATERIALS
Dovetailing with the emphasis on emissions was a focus on procuring the right materials for construction. Materials used contained Environmental Product Declarations and high levels of recycled content.
The selection of pre-engineered metal building and standard assembly measurements was also significant. And along with a landfill diversion strategy for excess materials on site, the project was able to limit total waste to less than 10 lbs per square foot with 90% of that material diverted from the landfill.
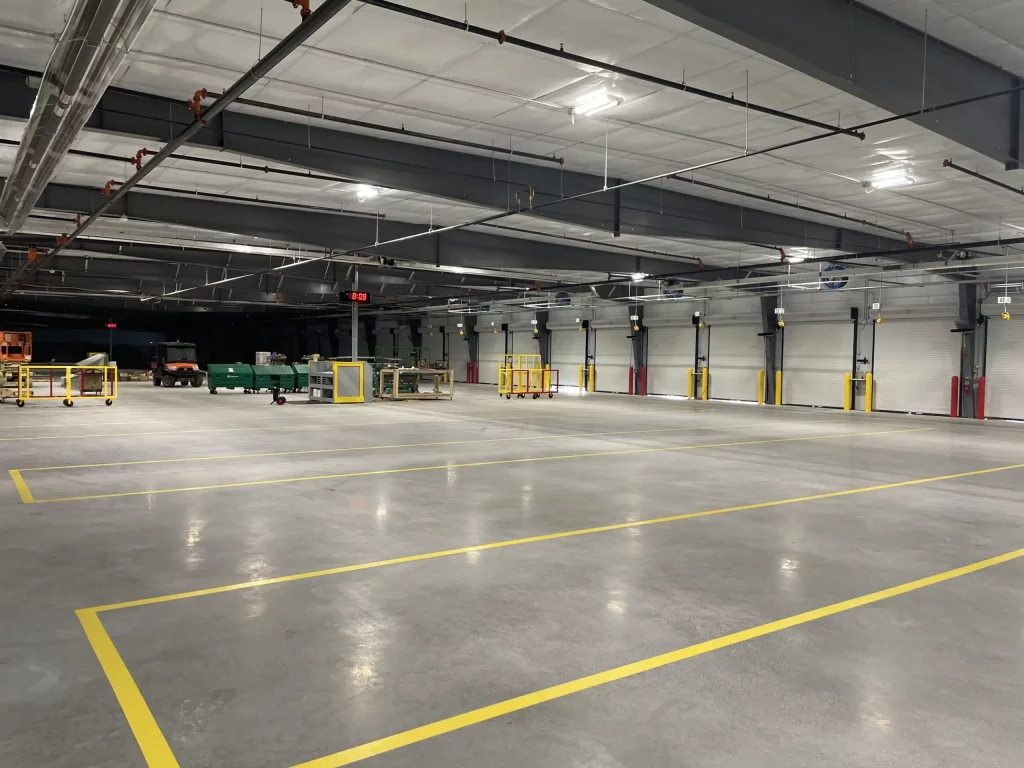
THE IMPACT
TRIPLE BOTTOM LINE
At the end of the project, the team chose to quantify what investment in LEED strategies returned to FedEx Freight. Measures across the sustainability spectrum – Site, Emissions, IEQ, and Materials for example – were analyzed using a Triple Bottom Line Analysis. This analysis quantifies the community, occupant, and operational cost impacts for green design and construction. For the 2% additional capital invested in LEED certification, a 26% triple bottom line was returned.
To underscore FedEx Freight’s commitment to greenhouse gas emissions reduction, over 10,325 metric tons of carbon dioxide equivalent (MtCO2e) were avoided through the systems and materials used in the project.
:: FEDEX FREIGHT FACILITY SUSTAINABILITY STATISTICS ::
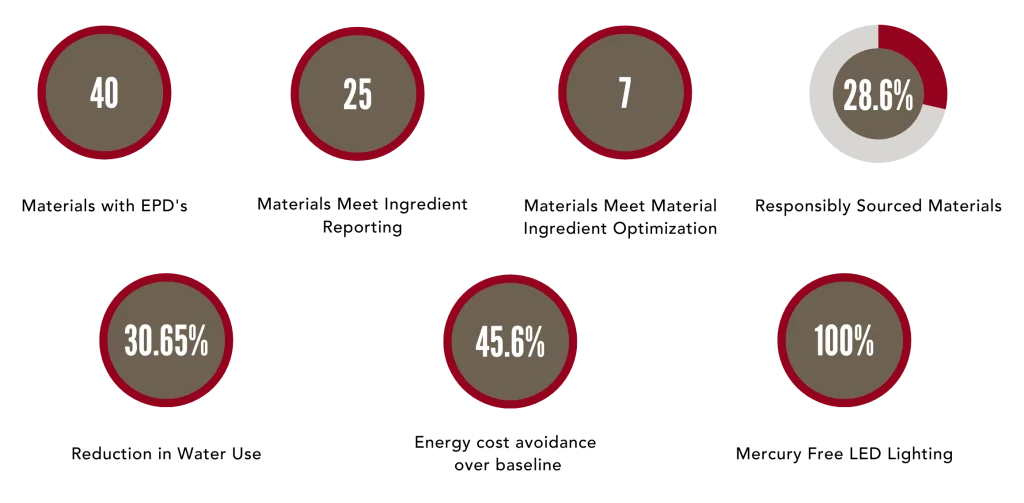
:: CASE STUDIES ::
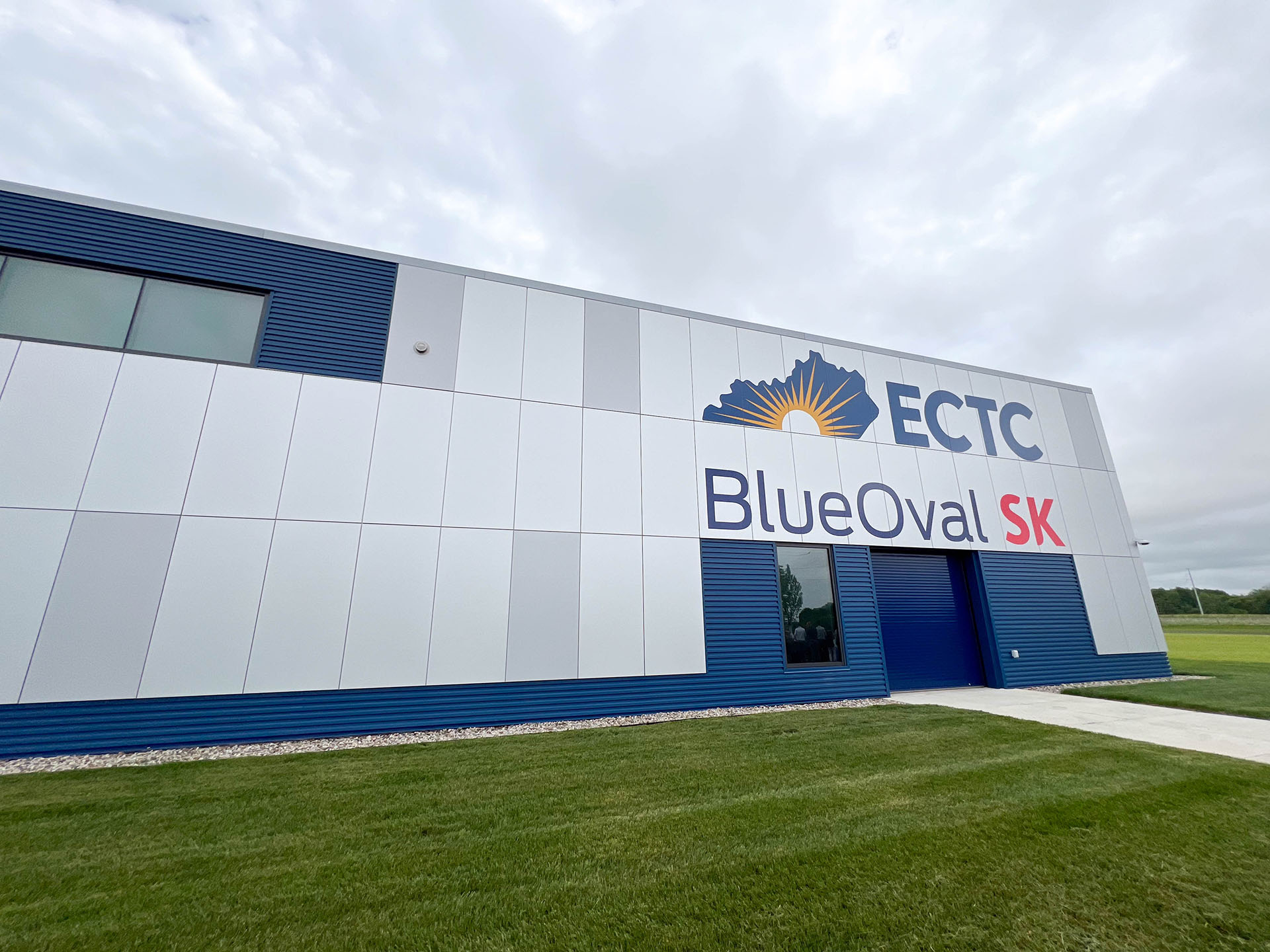
BlueOval SK Training Center
The 1,500-acre BlueOval SK Battery Park in Kentucky is a new battery manufacturing campus that produces batteries for future Ford and Lincoln vehicles. The park employs over 5,000 people who train for future careers at the 42,830-square-foot Elizabethtown Community and Technical College BlueOval SK Training Center. The center provides advanced on-site training, supporting a sustainable workforce and enabling Ford and SK On to maintain skilled labor within the region.
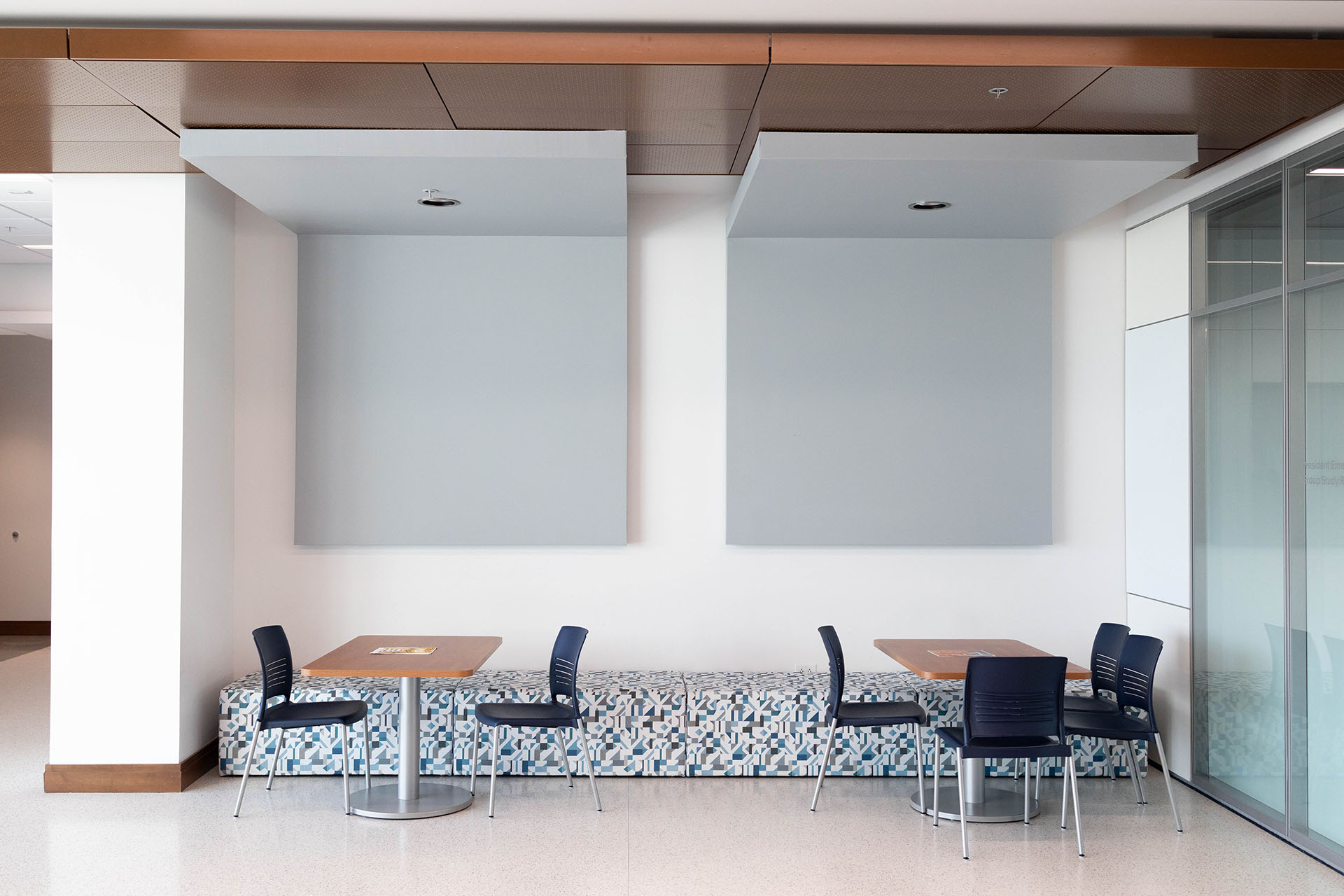
CMIT Building
Berea College envisioned two future-focused buildings to harness the power of computer science, digital media and information technology, and applied engineering and design to prepare the next generation of technology thinkers, makers, and innovators.
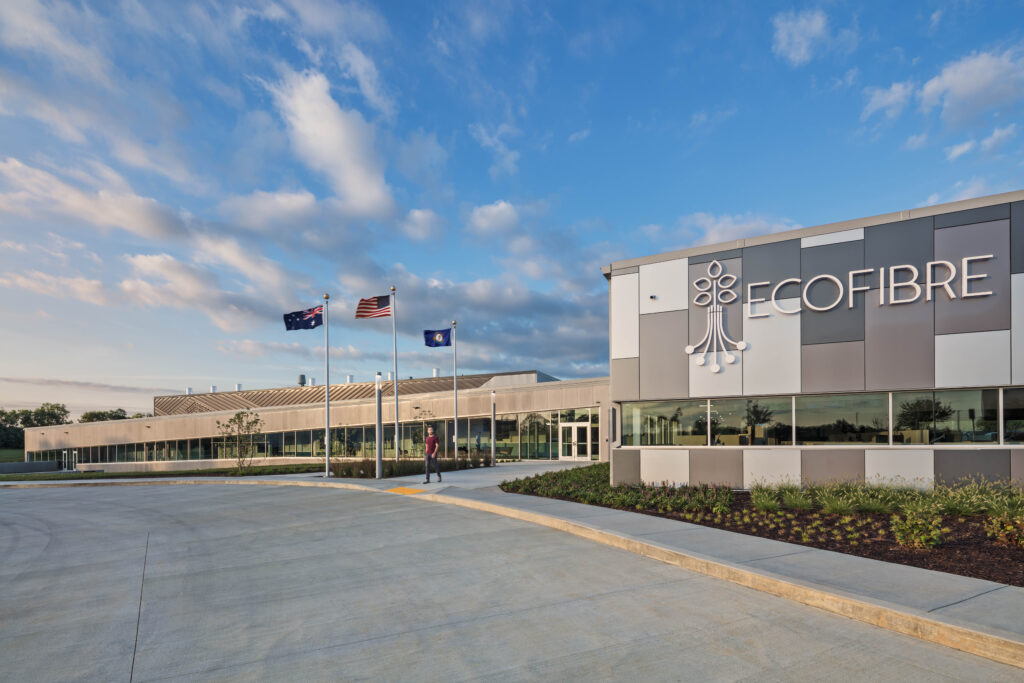
Ecofibre U.S. Headquarters
Discover how Ecofibre’s U.S. headquarters became the first LEEDv4 Platinum warehouse and distribution center, setting a new standard in sustainable building and innovative hemp-based products.
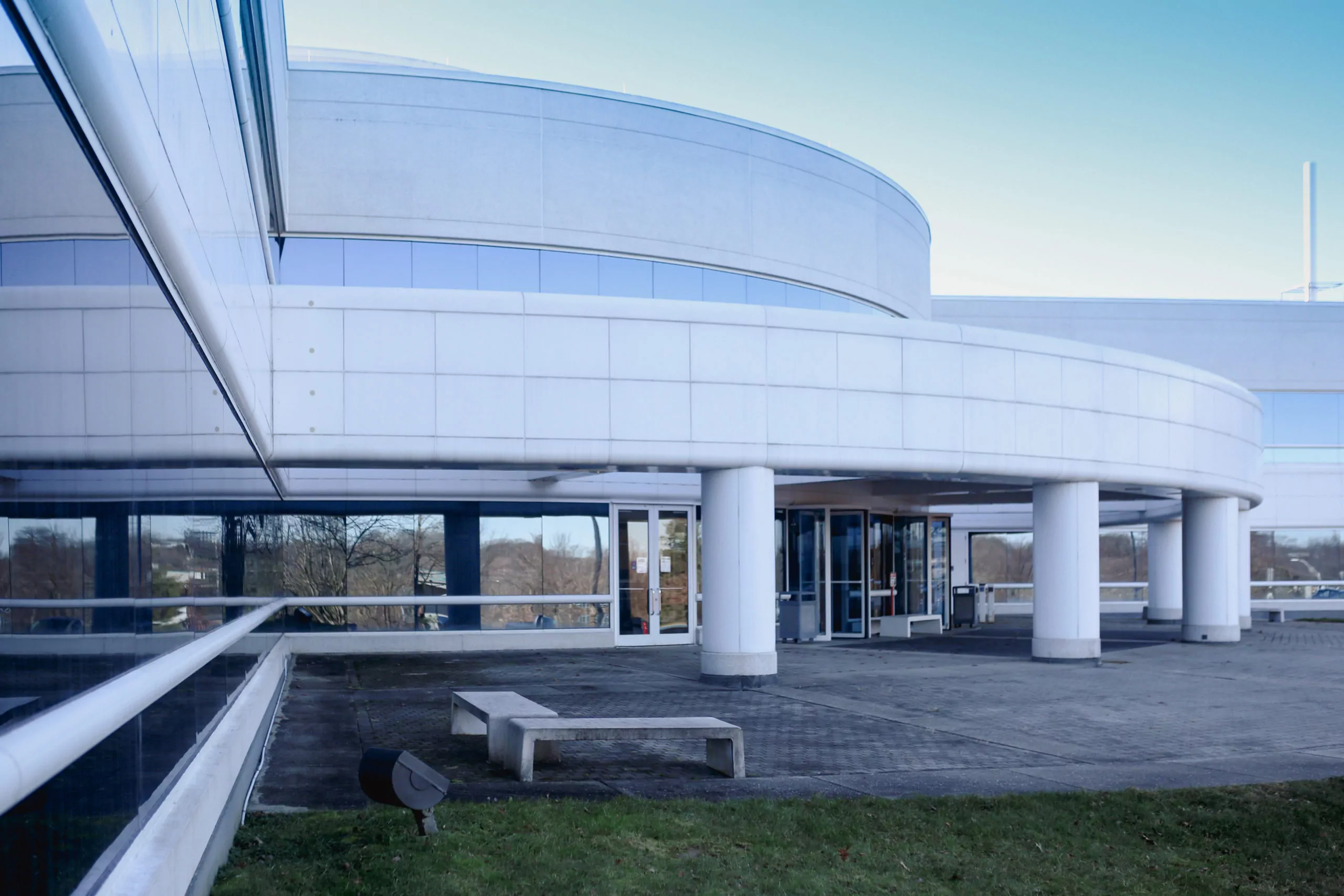
Centralized Lab
See how Paladin’s strategic interventions at a 1980s building have led to a 20% energy reduction over 10 years, preserving capital and optimizing operational efficiencies despite rising energy costs.
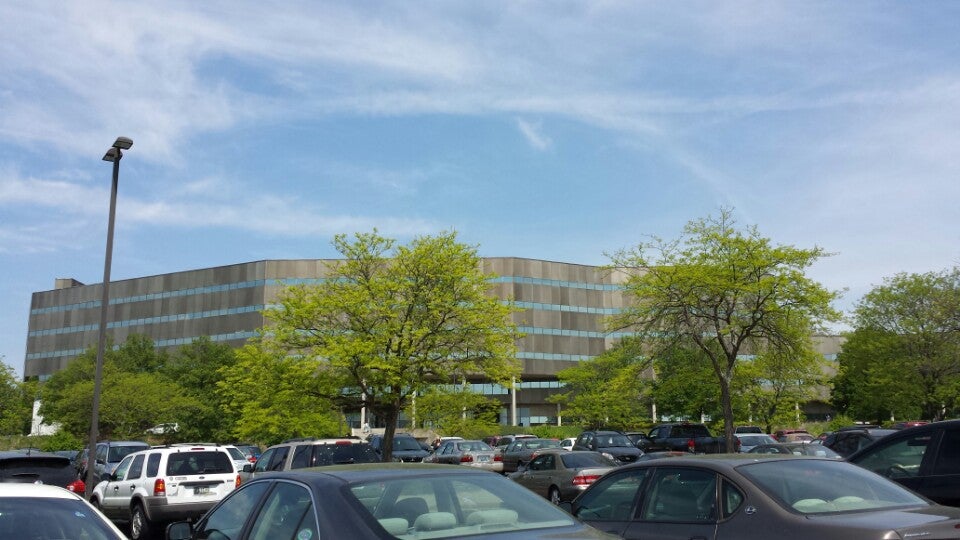
Cabinet for Human Resources Complex
Discover how the CHR Building achieved a 27% annual energy reduction, saving approximately $204,000 per year through strategic system enhancements and energy-efficient measures.
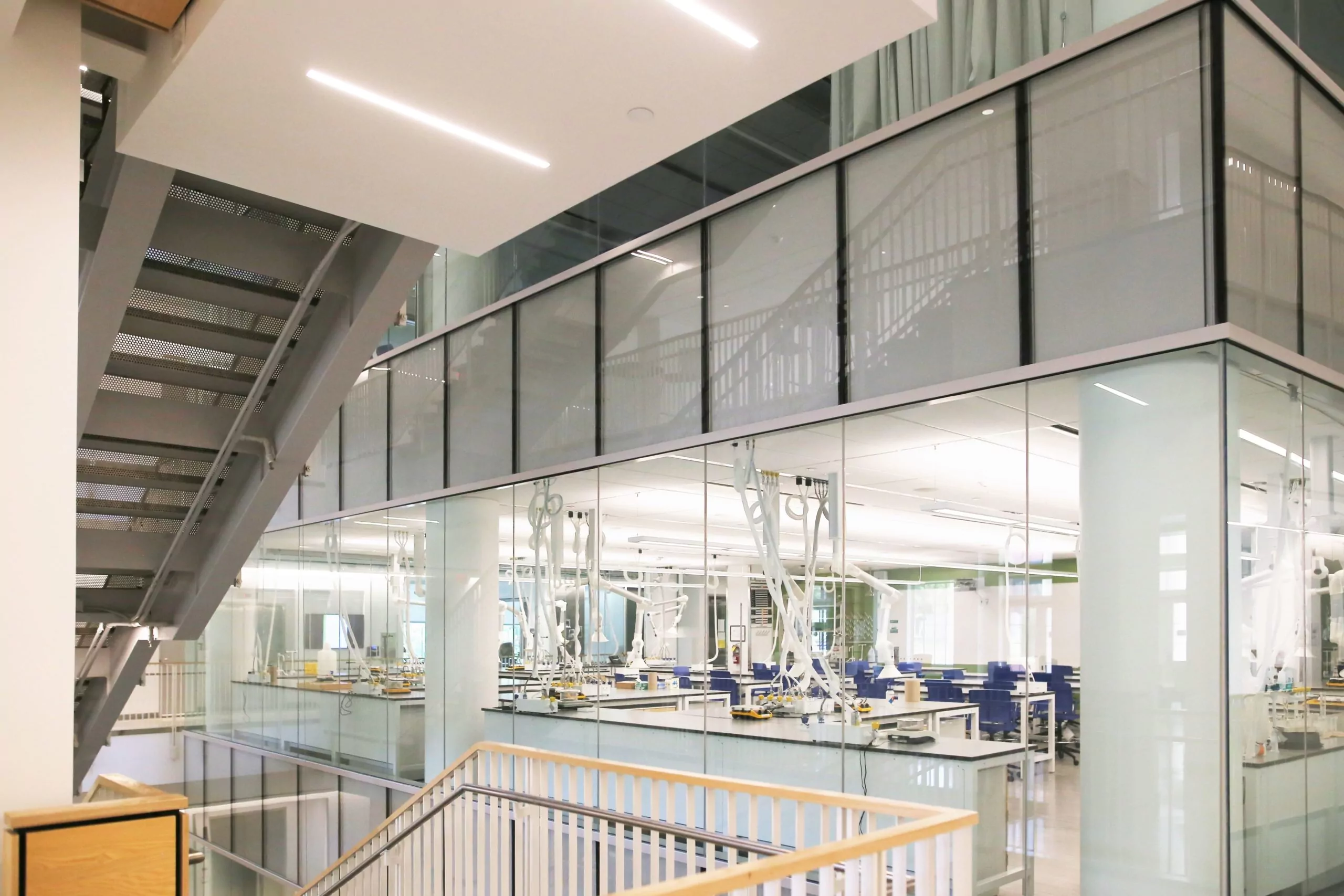
Berea Natural Sciences & Health Building
Explore how Berea College’s Natural Sciences and Health Building, a LEED Gold project, achieves optimal performance, energy savings, and a unique educational environment for advanced scientific learning.

Belknap Residence Hall Phase I
Discover the Belknap Residence Hall at UofL, where Paladin’s expert guidance led to LEED Gold certification, promoting sustainable living and learning with a significant 36.1% reduction in water use.

4th Street Live!
Explore the GSA Fit-Up project at 4th Street Live!, where Paladin’s expert sustainability strategies led to LEED certification, enhancing access to USCIS services while prioritizing environmental and operational efficiency.
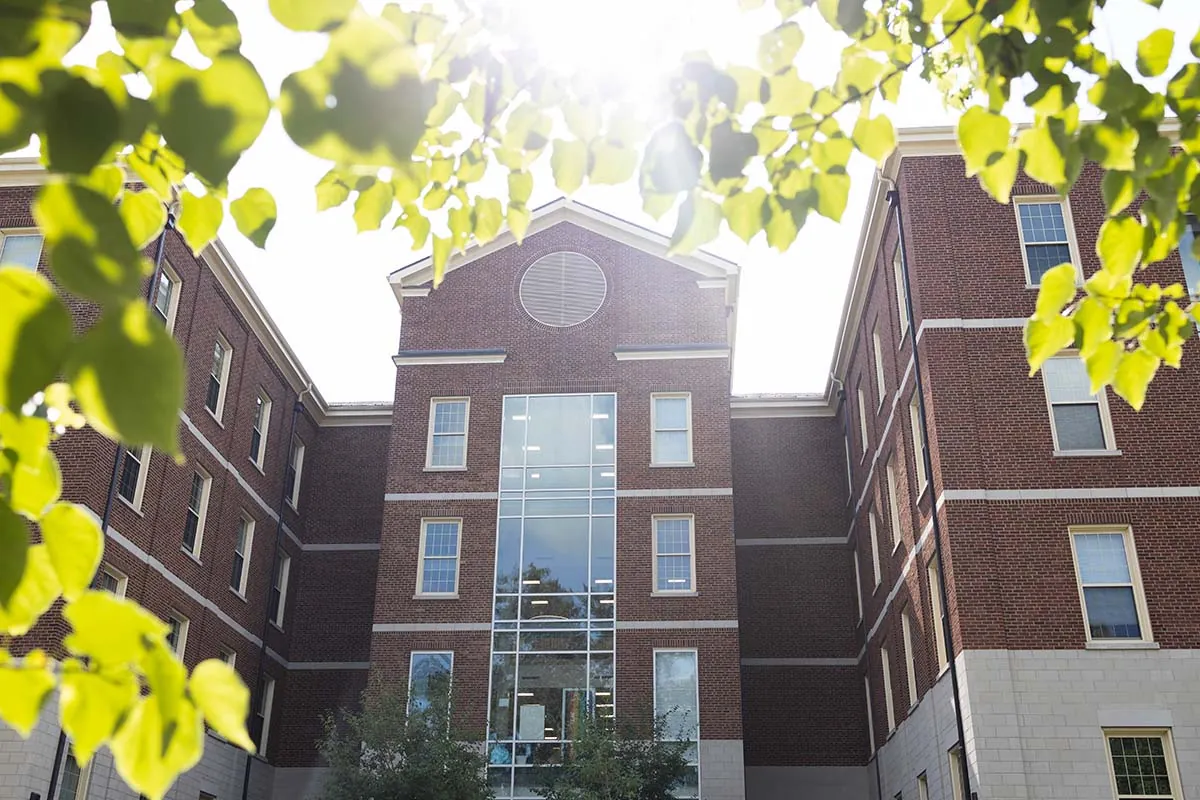
Danforth Hall and Kettering Hall
Discover Danforth and Kettering Halls at Berea College, where innovative design and sustainable construction earned LEED Silver certification and achieved a remarkable 48.1% reduction in water use.
:: CLIENT REVIEWS ::
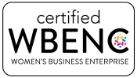
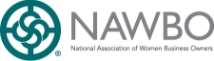
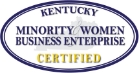
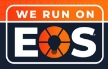
