By Erica Weeks, LEED Fellow
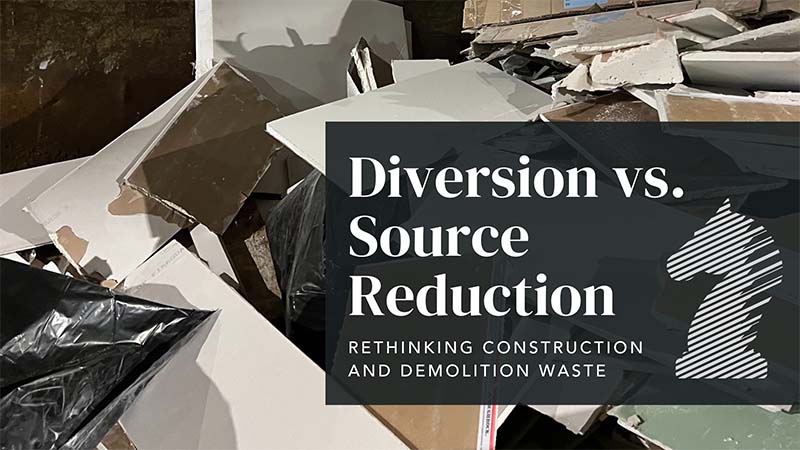
Construction and Demolition Waste in the Built Environment
Construction and demolition (C&D) waste is a necessary evil of an ever-changing built environment. Buildings outlive their useful lifespan and are demolished for new ones to take their place (I’ll discuss adaptive reuse of existing buildings at another time).
Delivering custom buildings requires custom fitting (custom cutting) of several materials throughout a design and construction process. Waste (whether recyclable or not) is inevitable, but there are steps to ensure that your project can minimize the impact.
The Role of LEED and Recycling for Waste Reduction
Since the early days of LEED, diverting waste from the landfill was a core imperative of creating a sustainable building project. Recycling is a good thing. Whenever a material can be taken as a waste product from one use and re-introduced into a “new” product as a raw material, you are reallocating those resources for their highest and best use. Many cities and states across the United States have implemented a variety of ordinances for minimizing C&D waste or requiring always recycling certain materials.
Challenges and Strategies in Recycling and Reuse
The recycling of demolition and construction debris can be complex and potentially time consuming. During demo, the materials that can be salvaged, recycled, reused, or repurposed first need to be identified. In a demo project, can materials be stacked and wrapped for manufacturer take-back programs? Are there materials that have value as recycled, such as metals? Are there entities that may want to repurpose materials that still have useful life? This identification process takes time and finding outlets for materials to be reused and repurposed can be a challenge. It’s a good “good,” but there may be no marketplace for its quick stock and resale. If the materials can be reused, careful demolition may be required to unfasten materials, stack them for transport, and leave the goods in working order. This also takes time, as compared to putting everything into the landfill dumpster in one fell swoop.
Construction Waste Management and Diversion Plan
When preparing for ongoing construction waste generated for new work, creating a detailed construction waste management and diversion plan can help identify market conditions and illuminate key materials that can be recycled or reused.
This process takes more than calling your local C&D waste hauler and ordering dumpsters. If you take a critical look at what may have reuse/resale value, you will find that there are outlets to repurpose some materials. This also takes a keen eye for the construction process and not only an understanding of how materials are installed but how they are delivered. For example, if your project has a lot of masonry goods, like brick or CMU, those are likely delivered to the site on wood pallets. Those wood pallets have likely only been used that one time, perhaps two, and instead of the pallets going into the dumpster to later become wood chips, we should ask, “Can the mason reuse them? Or is there another local vendor that wants to pick them up for no cost because they have re-sale value to others?”
Asking questions about the delivery process will start to unlock reuse or resale potential.
Diversion rates from the landfill have been cited for LEED credits as 50% and 75% diversion. Again, while diverting from the landfill is a good practice, it does not tell the whole story.
Source Reduction
In LEED v4 and v4.1, an optional metric around “source reduction” was introduced. This metric asked projects to limit the total waste/recycled material pounds per square foot that a project generated. Source reduction seeks to lessen any material from being discarded.
According to U.S. Green Building Council, source reduction is defined as “a decrease in the amount of unnecessary material brought into a building in order to produce less waste. For example, purchasing products with less packaging is a source reduction strategy.”
Why is this source reduction metric interesting? There are a few reasons:
New material that is discarded during installation has been bought by the owner. Paid for!
Once offcuts are discarded, the owner pays to haul them away to the landfill or to be recycled. Paid for!
New materials purchased have used energy from extracting their raw materials through the manufacturing process and via transportation to the project site, so embodied carbon – greenhouse gas emissions. Paid for!
Life of the product in the landfill – could be an eternity.
Evaluating Construction Waste Trends
In our study of a select group of LEED projects, we assessed our collected construction waste data to determine if a project’s diversion rate had any correlation to the type of building, construction, size of the building, and primary materials used. We took the data, converted it into pounds, and then pounds per square foot to gauge where we were most successful in reducing waste via source reduction.
Interestingly, the waste generated numbers (in pounds per square foot) are shocking. Even projects with high diversion rates for recycling produce significant waste.
- For example, a 3-story masonry building exceeded 80% diversion rate, but generated 24 pounds per square foot of waste materials.
- For example, a small interior fit-up project with many private offices exceeded a 50% diversion rate but generated 14 pounds per square foot of waste materials.
- Alternatively, a large warehouse distribution center exceeded a 90% diversion rate, and only generated less than 1 pound per square foot of waste.
Rethinking Waste Reduction Strategies
Different building types, the variety of construction materials on a project, and the installation practices need to be considered. Does this mean that as an industry we are not doing enough to pre-plan to eliminate waste to start with? Does the designer need to change how they think about the modules that materials are made, and how to specify best practices for the use of off-cuts or dimensions that can support modules? Do contractors need to provide input on how to eliminate waste generated and advise more frequently on delivery materials?
In LEEDv5 (which will be adopted in 2025), the limitation of pounds per square foot for the source reduction pathway points has been eliminated. LEED v5 still has requirements for diversion rates but now adds new requirements for single stream recycling or salvaging. Eliminating the source reduction strategy does not seem to get to the root of the issue – that there is too much waste, recyclable or not, being generated during demo and construction.
To truly move the needle on waste reduction, the industry must rethink not just how we manage waste, but how we design and build to minimize it from the outset.